In this series of seal design White papers, we will discuss the various aspects of tank seal design. We believe that by sharing our knowledge we will contribute to improving the overall knowledge of these safety-critical products. This will prevent safety incidents such as rim-fires and corresponding escalations. This way we aim to contribute, not only to an immediate emission reduction as well as prevent future pollution and injuries caused by these major incidents. The images and texts shown in these whitepapers are intended to serve as learnings for the prevention of future incidents and are by no means intended to discredit any supplier. The issues mentioned in the papers are universal and not limited to one supplier. This paper introduces an evaluation of compression shoe seals, which are gaining importance in our industry but have significant limitations in their use. This whitepaper addresses some technical concerns.
Introduction
Reliable evaluation of different seal designs is not easy, because there is no solid comparability of sealing systems. This results in ambitious and eager providers using the opportunity to offer technically inferior solutions with lower effectiveness and higher risk. They take advantage of the fact that the true efficiency of their systems can hardly be measured or evaluated. Tank owners on the other hand support this behavior by continuously opting for low-cost solutions over proven efficiency. this dangerous and unsustainable behavior is often promoted for quick monetary gain. An evaluation of the actual cost involved with poorly performing seals, however, shows that the cost of the seal choice goes far beyond the initial purchase. Only the cost of the lost product over the service life of the seal can be as much as 100 times that of the initial purchase of the seal
The effectiveness of the sealing systems today is measured worldwide by the methods of the API (Manual of Petroleum Measurement Standards, Chapter 19.2), which are essentially based on laboratory measurements in a short test channel.
The testing methods of amongst others API are for many reasons outdated, highly impractical, and do not do justice to the dynamic behaviour of storage tanks. Regard of these impracticalities some useful tests have been done that give proper insights
Tests by API
Primary seals extending into the storage liquid (liquid mounted) with close contact to the tank shell have 5-10 times lower emissions when compared to primary seals that do penetrate the stored liquid (vapour mounted). This is particularly relevant to external floating roofs, whose emission is strongly dependent on wind influences.
Soft tube seals with sealing body (flexible foam plus enveloping sealing membrane) have a significantly higher sealing effect when compared to shoe plate seals of the same contact height on the tank shell, caused by better matching of the soft-elastic sealing body to the irregularities of the tank shell.
The effect of shell contact height
Evaporation tests by the Swiss Materials Testing Institute EMPA

In a metal jar, half filled with petrol, round tubes were attached with different diameter and length. By measuring the emission from the different tubes it is possible to obtain a theoretical emission pattern of gasoline in open contact with the air. The graph of the measured daily emissions showed a clear dependence of the emission when compared to the diameter and length (height) of the tubes. the longer the tube, the smaller the emission.
This can directly be related to the efficiency of seal plates. Basically the longer the contact with the tank shell, the lower the emission regardless of gaps in the seal. Looking at the graph, a contact length of approximately 500mm should be sufficient to reach the lowest emission level. It is noteworthy to observe that the emission of a 29.1mm tube with a length of 500mm is not that far off a tube of 5.9mm. It can be concluded that gaps in primary shoe plates are a contributing factor to emission, but the length of contact above the product level has an even more profound influence.
First, some general explanations on the emission mechanism of tank seals.
- Assume through each stage of sealing the same amount of emissions (Etotal) penetrates.
- The emission resistance (RE) of the individual seal stages RE1, RE2 RE3 are different and addup to the total emission resistance of the system REtotal.
Emission is caused by two active forces.
- The vapor pressure of the stored liquid
- The ventilation or the wind acting on the sealing system.
For assessing the quality of a sealing system, the whole construction is to be regarded in two directions:
- In a vertical section through the annular gap,
- In tank shell circumference
The total emission resistance REtotal results from the emission resistance in vertical direction REv, multiplied by the emission resistance in tank circumferential direction REc, which is due to the imperfections of the contact elements to the tank wall and the unsealable folds of the sealing membrane, close to the tank shell.
In the images below with top view of the floating roof, the general problem of the dimensioning of the sealing membrane close to the tank wall is shown. This decides on the resistance of emission REc in tank circumferential direction.
It must be realized that all available sealing membranes are equipped with fabric reinforcements that allow no elastic lengthening or shortening and are annually subject to shrinking. This means that the membranes need to be provided in the tank circumferential direction with excess lengths, so that the seal can touch the tank wall everywhere, even if the floating roof is in eccentric position (+/- 100 mm to +/- 150 mm).
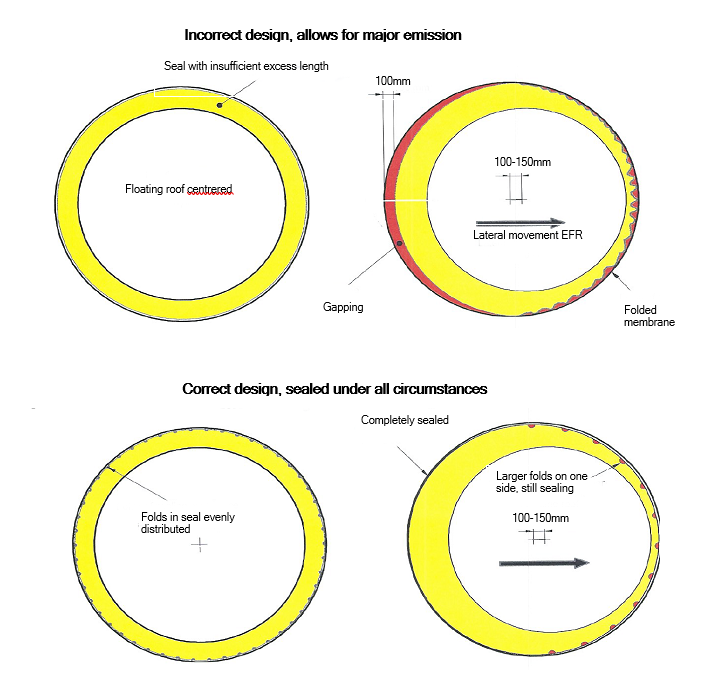
the effect of tank seal membrane efficiency
For a lateral movement of an average floating roof of 40m diameter by to 100 mm in any direction a 400mm excess length of the vapour barrier is required if no special construction aids are provided (pantograph attachment to shoe plates, pressing down of membrane folds etc.).
A significant part of the know-how of the seal supplier is in understanding this mechanism. This decides to a large extent on the quality of the sealing system. Unfortunately, monetary reasons often prevail above this technical evaluation
Looking at so-called compression shoe seals (basically bent plates with a membrane, listening to fancy trade names, such as seal-master) the above mechanisms are prominent. They combine a low and varying contact with the tank shell with very limited possibilities of expansion int the circumference of the tank. Where many suppliers will tell that these seals have large theoretical rim gap coverage (the buzz term -x/+3x is famous here) in practice, they do not live up to their promise. The vapour barrier limits the outward movement and the limited contact with the tank shell further reduces the efficiency in case of gaps. This combination makes the compression shoe seal one of the least efficient seal arrangements.
These systems have their use, but it is more limited than the commercial talks would make you believe.
For more insights, please contact us.